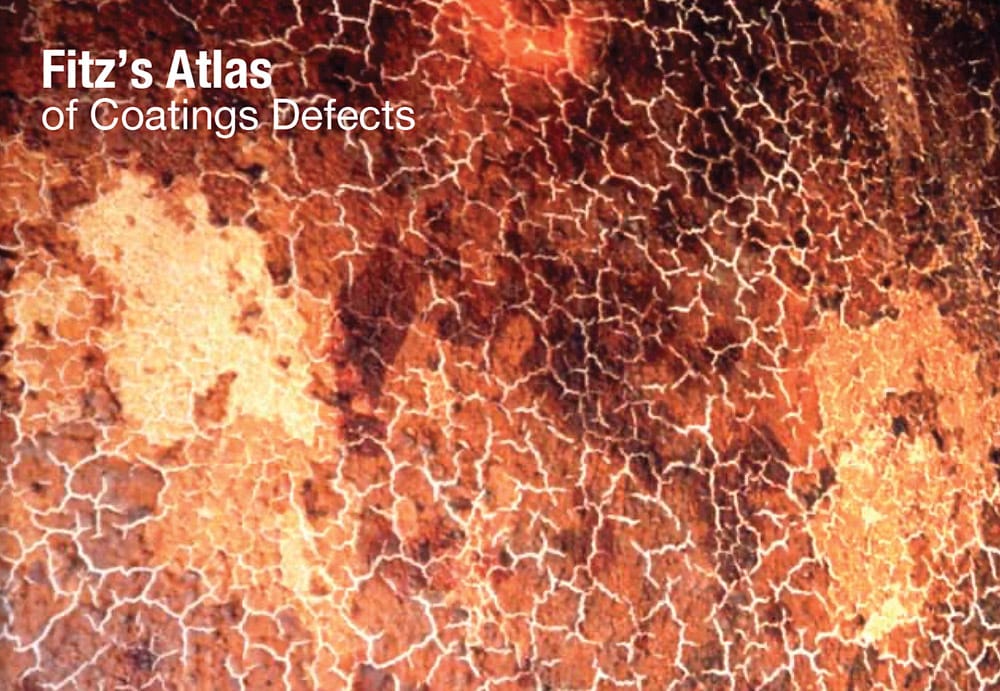
Fitz’s Atlas
of Coating Defects
Fitz’s Atlas of Coating Defects is a 200 page, pocket-sized ring binder including more than 190 illustrations to provide the most comprehensive visual guide to Coating and Surface Defects, this book is highly regarded for its capacity to identify coating failures and offer comprehensive insights into the possible causes of these issues, along with recommendations for their resolution. It is extensively employed by coating inspectors, surveyors, and technicians.
Each section has been compiled by Coating Specialists who understand Paint Coatings and their Application and as such will provide a useful pictorial reference to all who use and encounter Paint Coatings, their Defects and Failures. The Atlas is a 4¾” x 7¼” 250 page ring binder with detailed illustrations.
Fitz’s Atlas 2 covers 93 categories and contains a total of 237 high definition photographs, which cover Welding Faults, Surface Conditions, Coating Defects, Microscopy and Marine Fouling. Each defect generally contains several examples to give the applicator or inspector a thorough understanding of the coating failure. Select the categories listed here to get further details
WORLD LEADING REFERENCE, SINCE IT’S FIRST PUBLICATION IN 1996, FITZ ATLAS HAS GROWN TO BECOME THE MARKET LEADING GUIDE FOR COATING DEFECTS. CREATED BY COATING EXPERTS, IT PROVIDES INVALUABLE EXAMPLES TO HELP COATING APPLICATORS AND INSPECTORS TO IDENTIFY AND FIX COATING ISSUES.

Fitz’s Atlas Customer
COATINGS DEFECTS CONTENTS
COMMON DEFECTS AS THEY HAPPEN
Alligatoring
This sequence shows the formation of alligatoring
Rust Cracking
A simulation of a crack forming and the effect of water ingress
Rust Spotting
Rust spotting and subsequent staining of the coating system
DETAILED EXAMPLES AND GUIDANCE
A few examples taken from Fitz’s few examples taken from Fitz’s Atlas 2 of Coating
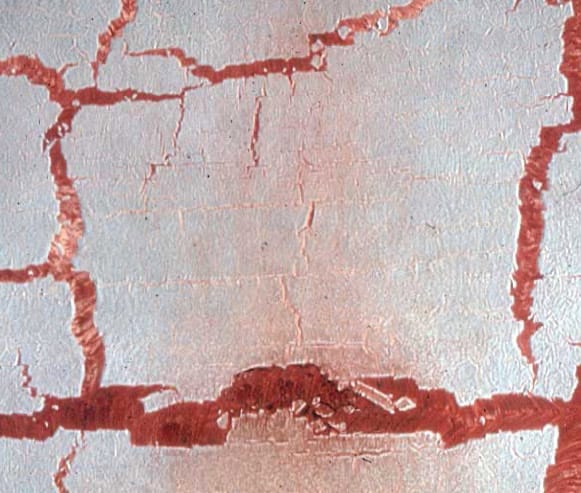
Alligatoring
Description
Very large (macro) crazing/cracking which resembles the skin of an alligator or crocodile. Cracks may penetrate through to the undercoat or down to the substrate.
Probable Cause
Internal stresses in the coating where the surface shrinks faster than the body of the paint film. Excessive film thickness and limited paint flexibility. Application of a hard topcoat over a more flexible softer undercoat. Application of topcoat before the undercoat has dried.
Prevention
Use correct coating specification and compatible materials. Avoid excessive film thickness. Avoid application at high ambient temperatures.
Repair
Repair will depend upon size and extent of alligatoring. Abrade or remove all affected coats and apply suitable undercoat and topcoat. Follow recommended application procedures.
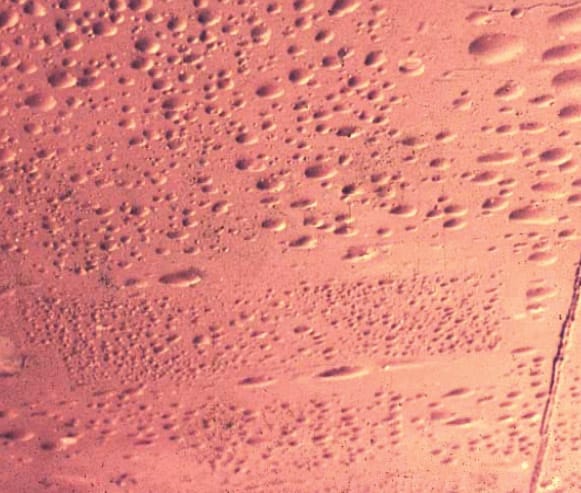
Blistering – Osmotic
Description
Dome shaped projections or blisters in the dry paint film through local loss of adhesion from an underlying coating.
Probable Cause
Osmotic blistering is commonly associated with the presence of soluble salts, soluble pigments, soluble corrosion products, retained solvents or the absorption and retention of low molecular weight water miscible solvents, typically from the carriage of chemical cargoes.
Prevention
Ensure correct surface preparation and application and follow working procedures for ventilation etc. Apply a suitable coating system after testing for soluble salts. Consider the possibility of the different blister mechanisms in the particular environment.
Repair
Depending upon size and type of blistering, remove blistered areas or entire coating system, fresh water wash and repair or fully recoat.